近日,深圳大学联合南京理工大学、香港理工大学以及上海交通大学在机械制造领域国际顶级期刊International Journal of Machine Tools and Manufacture上发表最新研究成果,揭示了伺服车削过程中伺服轴动力学误差对加工面型精度的影响机制,并提出了一种协同伺服切削新方法,在保证效率的前提下实现了轨迹跟踪和加工精度的大幅提升。深圳大学机电学院黄鹏助理教授为论文的第一作者。
基于金刚石刀具的刀具伺服技术已成为复杂光学元件超精密加工的主流技术之一,而切削运动精度直接决定了加工表面的精度。目前,几何误差对光学元件加工精度的影响已经得到了广泛的研究,而对于具有动态往复运动特征的伺服轴而言,更为重要的系统动力学误差对切削过程的影响却鲜有研究,这严重阻碍了对刀具伺服切削精度演变规律的基础认知。
研究团队以慢刀伺服(Slow tool servo,STS)为例,构建了耦合切削系统动力学和刀具-工件交互作用的切削表面生成模型,并在此基础上对复眼透镜阵列这一典型光学元件的加工过程进行了仿真分析。分析结果显示,刀具切削轨迹的高频成分将导致非常大的轨迹跟踪误差,甚至引起伺服系统共振(图1)。轨迹的相位滞后将导致与对刀误差类似的加工表面扭曲变形(图2)。当转速减小时,此误差随之减小,但加工效率也会大幅降低。
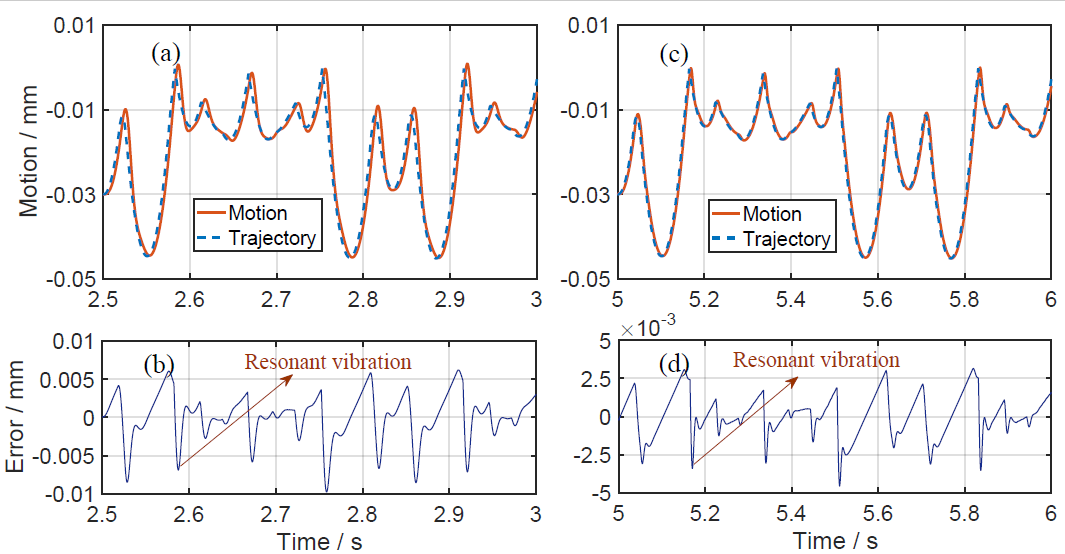
图1 主轴转速为30 rpm(a, b) 和15 rpm(c, d)的伺服运动和伺服跟踪误差

图2 微透镜阵列仿真加工表面(a)及其误差分布(b)
为了消除伺服轴动力学误差对加工精度的影响,研究团队提出了一种协同伺服切削新方法(cooperative tool servo,CTS),原理如图3所示。该方法创新性地使用具有高频响特性的快刀伺服(Fast tool servo,FTS)去实时跟踪补偿STS的伺服动力学误差。

图3 协同伺服切削原理
为验证CTS方法的有效性,研究团队以微透镜阵列为例,分别进行了数值仿真和实际切削加工实验。实验结果表明:在相同主轴转速下,相比于STS,CTS将轨迹跟踪误差的P-V值由4.8 µm降到了0.3 µm(图4),单个六边形微透镜单元的面形误差P-V值则由 4 µm降到了1.4 µm(图5)。上述研究结果表明,CTS能够非常有效地补偿STS加工中的伺服轴动力学误差,在相同效率情况下制造具有更高面形精度的复杂光学元件。

图4 CTS的协同伺服运动性能,(a) FTS 的轨迹跟踪,(b) CTS 的伺服运动误差

图5单个六边形透镜的面形误差( (a) STS和(b) CTS )
虽然此研究以微透镜阵列加工过程为例,但所提出的协同伺服切削(CTS)作为一种一般性的方法,对STS加工过程中的伺服轴动力学误差均能有效补偿,具有很好的通用性,在复杂光学零件的加工中具有非常广阔的工程应用前景。
原文链接:https://doi.org/10.1016/j.ijmachtools.2020.103556